Per qualsiasi taglio di precisione serve lo strumento giusto, adeguato al tipo di lavorazione che andrai a fare: questo strumento è l’inserto e il portainserto. In questo articolo vedremo quindi cosa sono, come funzionano e come scegliere l’inserto per tornitura corretto. Analizzeremo i diversi tipi di rivestimento e su quali materiali vanno usati, a seconda delle loro caratteristiche.
A cosa servono gli inserti per la tornitura e dove sono utilizzati
Durante il processo di tornitura il pezzo compie un moto rotatorio mentre l’utensile, avanza secondo un moto per lo più rettilineo. Il compito degli inserti è quindi penetrare nel materiale per asportare metallo, generando del truciolo.
Gli inserti possono essere impiegati per:
- tornitura interna: gli inserti lavorano internamente ad un pezzo cavo. In questo caso l’utensile per interno è chiamato barra di tornitura o per barenatura.
- tornitura esterna: agiscono esternamente ad un pezzo. A livello di nomenclatura, per capire qual è la dimensione dei porta-inserti per esterno è sufficiente leggere la parte finale del codice.
Gli inserti sono utilizzati in tutte le lavorazioni meccaniche. Li ritroviamo pertanto in officine in cui siano presenti torni semi automatici o manuali e macchinari automatici a controllo numerico.
Metallo duro dell’inserto: che cos’è, come si produce e come capirne la qualità
Gli inserti per tornitura sono realizzati in metallo duro, un materiale ottenuto tramite metallurgia delle polveri:
- particelle dure di carburi di Titanio, Tantalio, Niobio (Ti, Ta, Nb)
- particelle dure di carburo di Tungsteno (WC)
- un metallo legante, Cobalto (Co)
La realizzazione di un inserto in metallo duro prevede 4 fasi:
- produzione delle polveri: mediante processi di polverizzazione e atomizzazione, il materiale grezzo assume la corretta granulometria utile a passare alla fase successiva
- pressatura: per mezzo di uno stampo e di un maschio a spina conica, le polveri vengono compattate con una forza di pressatura che può variare tra
- sinterizzazione: il materiale pressato viene sinterizzato per mezzo di elevate temperature fino a ottenere un restringimento del 50%
- rettifica degli inserti: quest’ultima fase non va confusa con la riaffilatura. In generale, gli inserti in metallo duro sono creati con uno stampaggio di precisione rifiniti con processi di profilatura e smussatura. In alcuni casi gli inserti possono essere rettificati tramite mole diamantate: questo processo garantisce tolleranze molto strette.
Per capire come scegliere un inserto per tornitura valutane sempre la qualità, termine con cui si indica la tenacità o durezza dell’inserto. Le caratteristiche tecniche variano a seconda della combinazione delle sostanze che formano il substrato.
Come scegliere un inserto per tornitura in base al tipo di rivestimento
Per migliorare le prestazioni dell’inserto, il metallo duro viene rivestito da uno strato costituito nitruri di carburi e ossidi. Sebbene il suo spessore sia molto limitato (qualche micron), i vantaggi sono molteplici. Il rivestimento infatti incrementa:
- resistenza all’ossidazione
- isolamento e resistenza termica
- resistenza all’usura
- durata dell’utensile
- possibilità di usare paramentri di taglio più spinti
- scorrevolezza del truciolo
Sulla base del rivestimento, ci sono 3 tipi di inserti per tornitura: con rivestimento ad alto spessore, a basso spessore o senza rivestimento.
Rivestimento CVD (Deposizione chimica mediante vapore) – ALTO SPESSORE
Lo spessore raggiunge anche 20 micron e, nella maggior parte dei rivestimenti, è formato da strati di:
- Nitruro di Titanio – TiN: facilita il rilevamento dell’usura
- Carbonitruro di Titanio Ti(C,N): aumenta la resistenza all’usura sul fianco
- Ossido non ferroso – Al2O3: fornisce protezione termica
Dopo aver inserito le pile di inserti in una fornace, nella camera viene introdotta una combinazione di gas. La deposizione prosegue con una specifica serie di gas fino al completamento degli strati di rivestimento. Il processo è eseguito ad una temperatura di circa 900 °C per una durata di 30 ore.
Rivestimento PVD (Deposizione fisica mediante vapore) – BASSO SPESSORE
In questo caso lo spessore è di circa 3-6 micron. Il rivestimento è in nitruri di Titanio e Alluminio (TiAlN) e viene applicato a circa 500 °C. Rispetto agli inserti con rivestimento CVD, i PVD sono generalmente più tenaci. Vengono inoltre spesso usati in combinazione con substrati a grana fine per rivestire taglienti affilati.
Gli inserti vengono caricati nella camera di rivestimento in appositi vassoi. Sulle pareti della camera di reazione vengono sistemati dei target di metallo, di solito titanio. Questi vengono scaldati fino a raggiungere la temperatura di ionizzazione del metallo. Utilizzando un gas come vettore, gli ioni possono quindi essere trasportati dai target agli inserti e, dato che gli inserti sono più freddi, gli ioni si condensano sulla loro superficie fino a formare un rivestimento. Questo tipo di processo è di solito usato per la fresatura: lavorando con più taglienti in contemporanea aumenta infatti il tempo di raffreddamento ed è sufficiente quindi un rivestimento a basso spessore. In fase di finitura, inoltre, si riesce ad asportare poco materiale con poche pressioni e questo è un altro grande vantaggio dei PVD.
Inserti non rivestiti, ideali per taglienti molto affilati 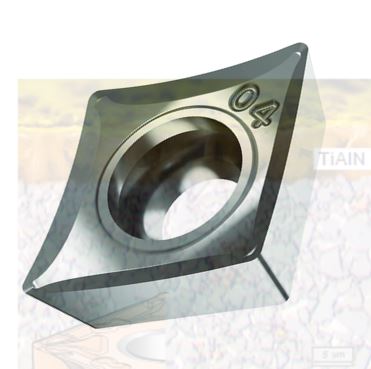
Ci sono lavorazioni che richiedono però l’utilizzo di inserti non rivestiti. Il rivestimento, infatti, rende il tagliente arrotondato e quindi non appropriata per il taglio di alcuni materiali non ferrosi.
Inoltre anche quando serve un tagliante estremamente affilato è bene che l’inserto non abbia alcun rivestimento, proprio per mantenere il massimo livello di affilatura.
Focus: classificazione dei materiali da lavorare
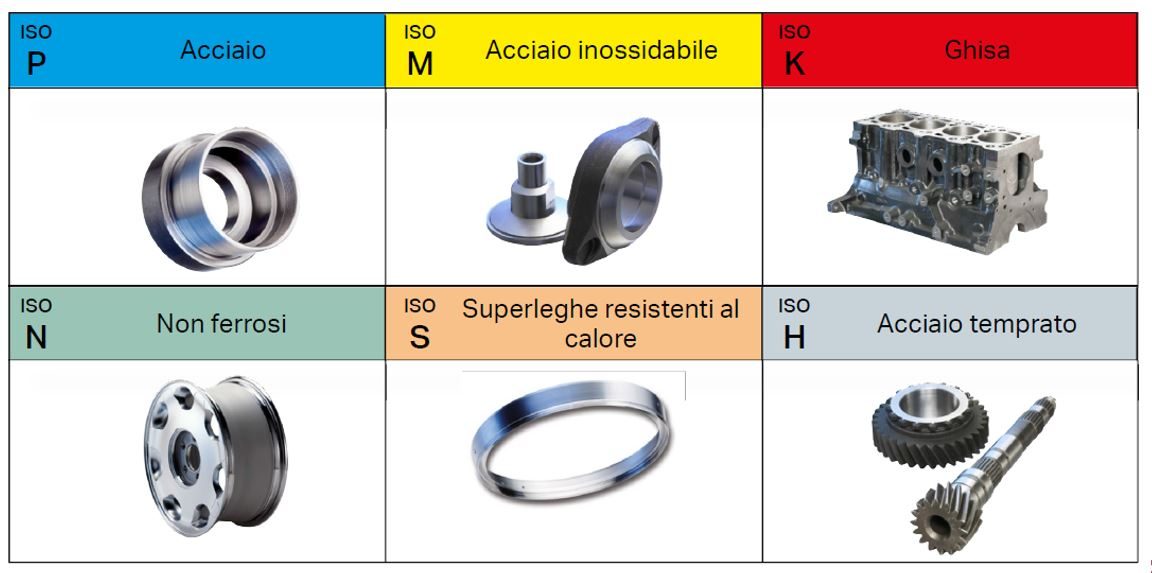
NB: I colori sono nomenclature ISO, quindi universali.