Sono tantissime le lavorazioni che si possono ottenere con la tornitura, un processo utilizzato da fabbri, serramentisti, carpenterie metalliche, tornerie, cantieri navali e in generale in tutte le officine dotate di torni manuali, semi-automatici o macchine automatiche. Vediamo allora nel dettaglio che cos’è la tornitura, come funziona e quali sono le principali tecniche.
Tornitura: che cos’è e a cosa serve
Semplificando al massimo, la tornitura è una lavorazione meccanica utilizzata per produrre pezzi con superfici assialsimmetriche. Il pezzo da lavorare viene reso solidale ad un mandrino e fatto ruotare. L’utensile da taglio, invece, si muove lungo il pezzo secondo un moto per lo più rettilineo, seguendo la direzione radiale o assiale oppure, per le superfici sagomate, spostando in entrambe le direzioni contemporaneamente. Il processo genera così la formazione e l’asportazione di truciolo che permette di dare al pezzo la forma desiderata.
Nel passato la tornitura era eseguita con utensili da taglio in acciaio HSS e inserti saldobrasati. Oggi invece si ricorre a inserti in metallo duro a fissaggio meccanico che permettono tagli di elevata precisione. La scelta quindi di un inserto o di un porta-inserto adeguati è fondamentale per la buona riuscita dell’operazione. Per capire qual è lo strumento più corretto devi sapere quale sarà l’applicazione di base per cui sarà utilizzato. Possono quindi esserci due tipi di lavorazione, che ora analizzeremo nel dettaglio: la tornitura esterna o interna.
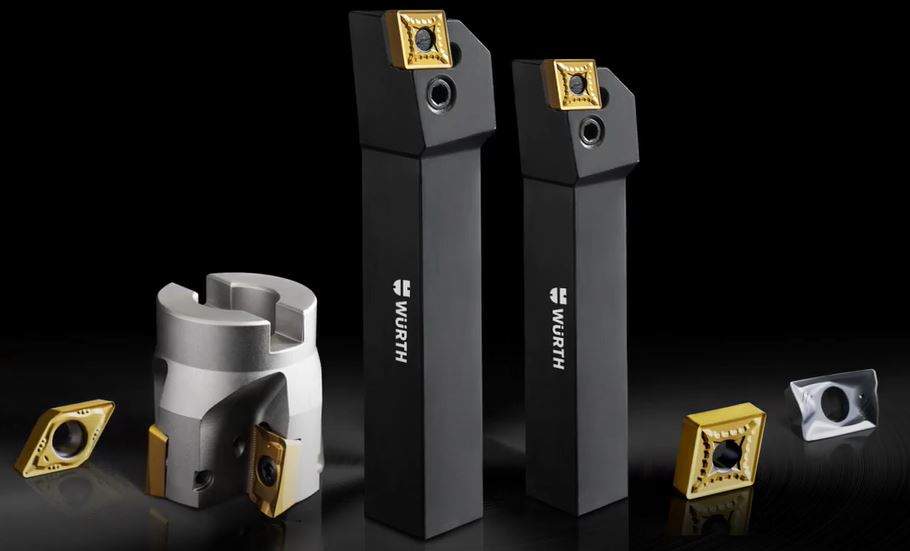
Tornitura esterna per modellare la superficie del pezzo proprio come vuoi tu
Si parla di tornitura esterna ogni volta che l’utensile da taglio agisce solo esternamente al pezzo, andando a sagomarne la superficie.
Le principali operazioni di tornitura esterna sono:
- Sfacciatura: l’utensile avanza radialmente per creare una superficie piana
- Tornitura conica: l’utensile avanza secondo la direzione angolata rispetto al pezzo creando una forma conica.
- Contornatura: l’utensile segue un contorno sagomato
- Tornitura di forma (formatura): l’utensile impartisce la propria forma al pezzo mediante un moto radiale
- Smussatura: si usa lo spigolo tagliente per eliminare l’angolo sul bordo
- Troncatura (cut off): serve per tagliare un’estremità
- Filettatura: tecnica con cui si filetta la superficie del pezzo in rotazione attraverso un utensile filettatore
- Barenatura: l’utensileria avanza linearmente sul diametro interno di un foro preesistente
- Foratura: si fa avanzare una punta forare con il pezzo in rotazione
- Godronatura: usata per produrre la zigrinatura sulla superficie del pezzo
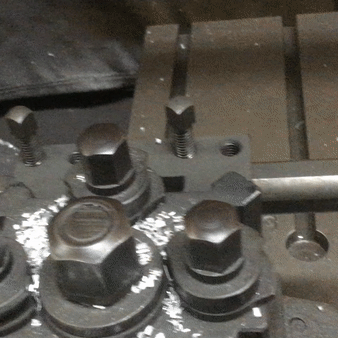
Ognuna di queste lavorazioni richiede quindi un utensile specifico per quel tipo di tornitura esterna.
Tornitura interna: come funziona e quali lavorazioni puoi ottenere
In questo caso l’utensile da taglio penetra nel pezzo, modellandone la superficie interna.
A seconda del tipo di operazione che devi realizzare potrai quindi avere degli utensili per:
- tornitura generica
- filettatura interna
- scalanatura
- tornitura dei profili interni

Quali parametri considerare per ottimizzare ogni operazione
Ora che abbiamo visto che cos’è la tornitura, vediamo quali sono i valori da prendere in considerazione per impostare il lavoro al meglio. I principali parametri, diversi a seconda del metallo da lavorare e della tipologia di utensile utilizzata, sono:
- velocità di rotazione del mandrino, si misura in giri al minuto e, per mantenere una velocità di taglio costante, va continuamente regolata in base al diametro di taglio (metri al minuto)
- velocità di avanzamento dell’utensile sul pezzo da lavorare (millimetri al giro)
- avanzamento: la distanza percorsa dall’utensile sul pezzo in lavorazione durante un giro di mandrino
- profondità di passata, ovvero la penetrazione dell’utensile nel pezzo che si misura in millimetri
Tutti questi parametri sono correlati tra loro e vanno scelti accuratamente in base al tipo di lavorazione, alle caratteristiche della specifica operazione ed in funzione all’applicazione. L’incremento di uno a svantaggio degli altri può garantire prestazioni più elevate piuttosto che finiture più spinte come anche durate degli utensili più consistenti. La fase di settaggio della lavorazione rappresenta l’attività più importante per l’esecuzione della lavorazione meccanica