Con il fissaggio diretto i tempi di installazione si riducono: ti basta una sola operazione per eseguire il fissaggio e non hai bisogno di preparazioni preliminari.
Per una corretta esecuzione è importante però avere gli strumenti giusti. Servono inchiodatrici adatte, chiodi specifici e adeguate lattonerie sagomate a fissaggio diretto. È poi anche fondamentale sapere su quali materiali operare e come eseguire il fissaggio al meglio.
Approfondiremo tutto in questo articolo!
I vantaggi del sistema di fissaggio diretto
La scelta del sistema di fissaggio è determinante in qualsiasi posa in opera. Le alternative da considerare sono soltanto due, per qualsiasi installazione, dall’edilizia alla lattoneria: fissaggio diretto o indiretto.
Scegliere il fissaggio diretto significa prima di tutto risparmiare tempo. Utilizzando una inchiodatrice dotata di caricatore puoi infatti eseguire numerosi fissaggi in pochi minuti. Oltre che veloce, questa operazione è anche semplice e, con i prodotti adeguati e lattonerie sagomate a fissaggio diretto, richiede uno sforzo minimo.
Inoltre il fissaggio diretto si presta a molteplici lavori e settori. Gli elettricisti possono ad esempio usarlo per l’inserimento di canaline per tubi o cavi. I cartongessisti per applicare staffe, rinforzi o casseri. E i carpentieri edili per ancorare profili di acciaio. Infine il fissaggio diretto può essere impiegato su vari materiali, dal calcestruzzo all’acciaio, e questo lo rende ancora più versatile.
Guida alla scelta della giusta inchiodatrice per un fissaggio diretto a regola d’arte
A seconda del materiale su cui lavorare e del tipo di operazione da svolgere esistono diversi tipi di inchiodatrice.
Una prima differenza riguarda la modalità con cui viene inserito il chiodo, a sparo o tramite spinta a pistone. Le inchiodatrici a sparo sono vietate nei cantieri. L’energia generata viene infatti interamente trasferita sul chiodo, rendendole così pericolose. Con la spinta a pistone, sul chiodo viene invece trasferito solo il 5% dell’energia dello sparo. Il restante 95% è controllato dal pistone che, rimanendo all’interno dell’apparecchio, non rappresenta un pericolo per l’utilizzatore.
Esistono poi:
- inchiodatrici a propulsori: semiautomatica, leggera e compatta, non affatica ed è ideale anche per un utilizzo in spazi ristretti
- inchiodatrici a gas: alimentata da cartucce a gas, è indipendente da impianti ad aria compressa e non è collegata a tubi d’aria. Quindi nessun intralcio e massima libertà di movimento
- inchiodatrici a batteria: leggera e autonoma, non necessita di cartucce a gas, propulsori o aria compressa
Come scegliere propulsori e forza di carica in base al tipo di materiale:
Ogni inchiodatrice necessita di specifici propulsori che devono essere indicati sul libretto di istruzione.
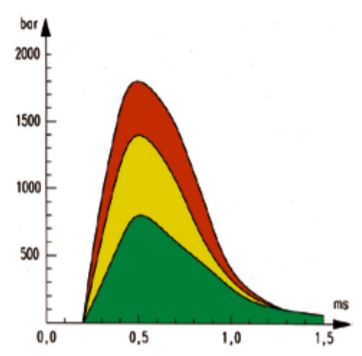
COLORE | FORZA DI CARICA | MATERIALE |
Verde | leggera | Calcestruzzo fresco (tempo di indurimento < 28 giorni), pietra calcarea |
Giallo | media | Calcestruzzo C12/15 – C35/45 |
Rosso | forte | Calcestruzzo C35/45– C45/55, acciaio con resistenza alla trazione fino a 450 N/mm2 |
Lavorare in sicurezza con responsabilità e la giusta inchiodatrice
Un’inchiodatrice professionale deve rispondere a particolari requisiti. Prima di tutto deve aver superato un severo test di sicurezza che accerti che, in fase di caduta, l’inchiodatrice non si avvii.
Deve inoltre entrare in funzione solo se appoggiata perpendicolarmente al supporto e non con la semplice pressione.
Per eseguire un fissaggio diretto sicuro affidati quindi solo ad inchiodatrici che abbiano:
- Numero di serie
- Marchio di omologazione
- Nome o marchio del fabbricante
- Certificazione
- Descrizione dei propulsori prescritti
Anche chi utilizza lo strumento deve farlo con responsabilità, indossando i corretti DPI e applicando tutte le dovute precauzioni. Deve inoltre conoscerne il funzionamento e i possibili pericoli legati all’utilizzo.
Fissaggio diretto su calcestruzzo: la qualità del sottofondo fa la differenza
La buona riuscita di un fissaggio diretto nel calcestruzzo dipende molto dalla qualità del calcestruzzo stesso e soprattutto dalla sua resistenza alla compressione. Più la classe di resistenza alla compressione è alta, più è adatta ad un fissaggio diretto. Quindi il sottofondo ideale per questo tipo di applicazione appartiene alla classe C100/C115 o simili.
Durante l’inserimento, il chiodo penetra nel calcestruzzo, spinge il materiale verso i pori vuoti circostanti e genera una compattazione del materiale. Inoltre, l’alta velocità con cui avviene l’inserimento del chiodo, produce calore, che favorisce la sinterizzazione dei due componenti, chiodo e calcestruzzo. In pratica i due materiali si accoppiano e compattano tra loro, rendendo il fissaggio ancora più solido.
Attorno al chiodo si forma quindi una zona altamente compressa e resistente. Il punto più fragile e a rischio frattura è invece all’interno del calcestruzzo. Ecco perché è importante che la superficie di penetrazione del chiodo sia corretta.
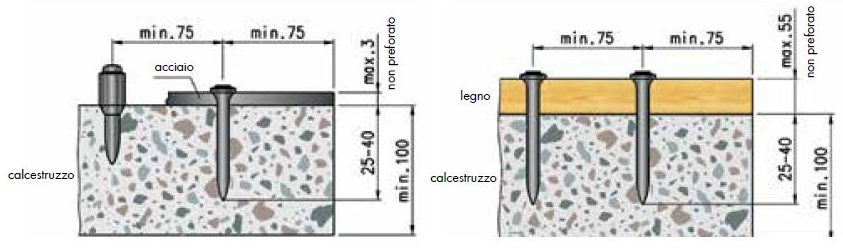
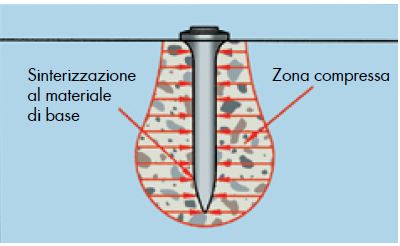
Fissaggio diretto su materiali leggeri tramite fissaggi multipli
Il fissaggio diretto può comunque essere praticato anche su rivestimenti leggeri per controsoffitto o soffitto. In questo caso bisogna però ricorrere ad un fissaggio diretto multiplo e non singolo.
Il vantaggio è questo: nel fissaggio singolo, se si verifica un cedimento o uno slittamento, si avrà la rottura di un unico punto. In un fissaggio multiplo, invece, ci sono almeno due punti di ancoraggio quindi, se uno dovesse cedere, il carico verrà comunque sorretto dagli altri.
Il sottofondo deve però essere abbastanza rigido per poter reggere i carichi e sopportare le deformazioni
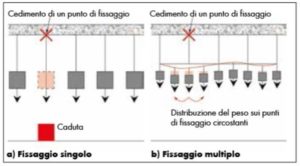
Fissaggio singolo o multiplo
Fissaggio diretto su muratura: è tutta questione di spessore
Non sempre è possibile applicare un fissaggio diretto su un sottofondo in muratura. Tutto dipende dalle dimensioni dei mattoni e da una serie di calcoli da fare.
Innanzitutto la profondità minima di penetrazione nella muratura deve essere di 25-40 mm. Inoltre tra il punto di entrata del chiodo e la fuga successiva devono esserci ameno 35 mm.
Ed infine questo tipo di fissaggio non va mai effettuato nel primo mattone all’angolo della muratura.
Vanno quindi evitati mattoni forati, superfici troppo dure, fragili o sottili e anche punti di entrata di precedenti foraggi.
I sottofondi che più si prestano ad un fissaggio diretto sono invece i mattoni pieni o calcarei e il calcestruzzo secondo la DIN 1045 e DIN EN 203-1.
Fissaggio diretto su acciaio: solo se fini e non legati
Le proprietà dell’acciaio cambiano a seconda dei materiali che lo compongono e le loro percentuali. Variano in particolare in base alla quantità di calcare a carbon coke introdotte nell’altoforno.
Non tutte le tipologie di acciaio si prestano quindi a fissaggi diretti.
I due tipi di acciaio idonei a questo tipo di fissaggio sono gli acciai a grana fine gli acciai da costruzione non legati direttamente.
Ad ogni fissaggio diretto, il giusto chiodo
Ogni tipo di fissaggio diretto richiede un chiodo di una specifica lunghezza che si calcola sommando la profondità di penetrazione alla componente da fissare.
Nel caso di fissaggi diretti su calcestruzzo la profondità di penetrazione va da 25 a 40 mm, sull’acciaio da 8 a 12 mm. Nel caso di sottofondi in acciaio si consiglia comunque di usare chiodi il più corti possibili tenendo conto che la profondità di penetrazione minima per sottofondi più spessi di 12 mm è di 10 mm.
Catalogo Fissaggio diretto
Sfoglia il catalogo per conoscere tutti gli articoli della gamma che possono fare al caso tuo >