Il rispetto dei principi ergonomici rientra all’interno delle misure generali di tutela elencate nell’art. 15 del D. Lgs. 81/2008 – Testo Unico sulla Salute e Sicurezza sul Lavoro.
Le disposizioni si riferiscono all’organizzazione del lavoro, alla concezione dei posti di lavoro, alla scelta delle attrezzature e alla definizione dei metodi di lavoro e produzione e hanno l’obiettivo di ridurre gli effetti sulla salute del lavoro monotono e ripetitivo.
L’articolo 168 del Testo Unico prevede anche che il datore di lavoro adotti le misure organizzative necessarie e ricorra ai mezzi appropriati – attrezzature meccaniche – per evitare la necessità di una movimentazione manuale dei carichi da parte dei lavoratori.
Idoneità con prescrizione: come gestirla?
L’art. 41.6 del Testo Unico prevede che il medico competente, sulla base dei risultati delle visite mediche, possa esprimere un giudizio di idoneità, idoneità parziale con prescrizioni o limitazioni, inidoneità temporanea oppure inidoneità permanente alla specifica mansione che il lavoratore è chiamato a svolgere. Nel caso di giudizio di idoneità con limitazioni (idoneo con limitazioni MMC) il lavoratore è ritenuto sostanzialmente idoneo alla mansione cui è preposto, seppur con delle precise limitazioni nell’esercizio della stessa al fine di tutelare la sua salute.
La gestione delle idoneità con prescrizione può risultare molto onerosa per le aziende, a causa delle difficoltà organizzative e di gestione della produzione collegate.
Inoltre, talvolta il medico competente non dispone di informazioni dettagliate: accade di conseguenza che egli rilasci idoneità con prescrizione, preferendo un giudizio cautelativo, o che al contrario venga rilasciata un’idoneità con prescrizione, quando questa sarebbe in realtà una inidoneità.
Considerando quindi che il giudizio di idoneità con prescrizione risulta essere spesso un costoso rimedio per risolvere situazioni non correttamente analizzate ed equivocate, è indispensabile ripartire da un processo valutativo più articolato, che coinvolga diversi attori aziendali, innanzitutto il lavoratore e a seguire tutti gli attori dell’organizzazione preposti alla sicurezza: datore di lavoro, RSPP, MC, RLS.
Obblighi del datore di lavoro
Come valutare i rischi per la movimentazione manuale dei carichi?
L’art. 168 del Testo Unico impone al datore di lavoro di adoperarsi, con misure organizzative e mezzi appropriati, per evitare la movimentazione manuale dei carichi da parte dei lavoratori o, nel caso in cui ciò non sia possibile, per ridurre il rischio derivante da tale movimentazione.
Ogni scelta a livello organizzativo-gestionale presuppone in via preliminare l’analisi e la valutazione dei rischi che la movimentazione comporta: in base alle condizioni specifiche di ogni realtà, dell’identificazione del rischio e del prolungarsi dell’attività di MMC, esistono metodologie idonee alla corretta valutazione.
Per affrontare tale analisi, l’articolo 168 rimanda esplicitamente all’allegato XXXIII, che fornisce indicazioni ulteriori in materia; in particolare, espone i principi tecnici di riferimento per progettare e gestire le attività, per individuare i fattori di rischio e i criteri di miglioramento. Oltre a quanto indicato in tale allegato, la norma indica quali altri punti di riferimento le norme tecniche, le buone prassi e le linee guida.
La valutazione semplificata delle condizioni di lavoro e di rischio
Tale valutazione va effettuata in tutte le postazioni di lavoro ove si svolga movimentazione manuale dei carichi e ove vi sia l’identificazione di rischio ergonomico, allo scopo di verificare la conformità dei posti e degli ambienti di lavoro ai requisiti minimi riportati nell’allegato XXXIII, prerequisito essenziale per il contenimento dei diversi fattori di disagio e di rischio per la salute e il benessere dei lavoratori.
L’elaborazione critica dei dati raccolti attraverso l’applicazione delle “check list”, oltre a rappresentare il primo passaggio fondamentale per l’ottemperanza a quanto previsto dal dettato normativo può condurre più nello specifico a:
- verificare nel dettaglio tutte le situazioni che, per uno o più aspetti, risultano non conformi rispetto all’analisi ergonomica e alle previsioni dell’allegato XXXIII
- pianificare gli interventi correttivi, per lo più strutturali, identificando priorità e costi connessi
- far emergere situazioni in cui, a causa di variabili organizzative (tempi di lavoro molto prolungati) e/o ambientali (es. difficoltà strutturali) problematiche, è necessario procedere a un approfondimento dell’analisi delle condizioni di rischio con più ampio ricorso alla parametrazione e misurazione degli elementi di rischio.
La valutazione approfondita delle condizioni di lavoro e di rischio
Il semplice esame di conformità alla prescrizione dell’allegato XXXIII risulta inadeguato per un’esauriente valutazione dei rischi di affaticamento fisico connessi all’attività lavorativa per le situazioni in cui la movimentazione manuale dei carichi sia:
- costante o ripetuta nel tempo
- prolungata sostanzialmente per l’intero turno di lavoro
- caratterizzata da compiti richiedenti azioni ricorrenti (fisiche, sensoriali e cognitive).
È necessario procedere a una valutazione più approfondita delle condizioni di lavoro e di eventuale rischio di sovraccarico per l’apparato muscolo-scheletrico, basandosi su un ventaglio più ampio di rilevazioni e misurazioni tanto di variabili fisico-ambientali che prestazionali.
I dati vengono raccolti anche attraverso rilievi mediante l’applicazione dei sistemi motion capture inerziali, attraverso l’analisi integrata di tutti i distretti corporei (arti superiori, rachide e arti inferiori).
La norma ISO 11228
Nel trattare il complesso degli elementi da considerare nella valutazione del rischio di patologie da sovraccarico biomeccanico connesse alle attività lavorative di movimentazione manuale dei carichi, l’allegato XXXIII del D. Lgs. 81/2008 fa esplicito riferimento alla norma ISO 11228. Tale norma è suddivisa in tre parti, che trattano rispettivamente sollevamento e trasporto, spinta e traino, movimentazione di bassi carichi ad alta frequenza.
Già da una prima analisi risulta evidente come questa definizione non comprenda solo la movimentazione intesa quale spostamento di oggetti da un punto all’altro, bensì un insieme di gesti, mansioni, compiti molto più ampio, che riguarda anche altre attività quali, a titolo esemplificativo, trasporto, sollevamento, sostenimento di carichi.
Di conseguenza, la valutazione del rischio risulta particolarmente complessa, in quanto è necessario tenere in considerazione tutte le azioni, che in fase valutativa si traducono in variabili, e agire su di esse per minimizzare il rischio per i lavoratori: la frequenza del sollevamento, il punto di prelievo e di deposito del carico, la sua collocazione, solo per citarne alcune.
La frequenza dell’azione
Questi casi, che vedono la commistione tra rischio da movimentazione manuale dei carichi e rischio da movimenti ripetuti, richiedono particolare attenzione in quanto comportano delle difficoltà non soltanto in fase valutativa ma anche nella successiva fase di intervento sulle variabili stesse: agire sulla frequenza di sollevamento, ad esempio, potrebbe ridurre il rischio da ripetizione, ma incidere negativamente su fattori di forza e forma, poiché potrebbe presentarsi la necessità di aumentare l’entità del carico per evitare decrementi di produzione.
L’esempio rende palese che l’intervento su casi di questo genere risulta complesso, a causa della numerosità delle variabili e della connessione tra le stesse; talvolta purtroppo l’azione porta a risultati ininfluenti dal punto di vista della protezione e prevenzione sul lavoro. Proprio perché l’eliminazione del rischio può dimostrarsi difficoltosa, spesso risulta necessario agire sulla problematica alla radice, rivalutando l’intera organizzazione aziendale e intervenendo sulla logistica lavorativa.
A cura dell’Ing. Lorenzo Baraldo, Direttore di Area per Contec AQS, società del Gruppo Contec che si occupa di salute e sicurezza nei luoghi di lavoro, tutela dell’ambiente e sistemi di gestione.
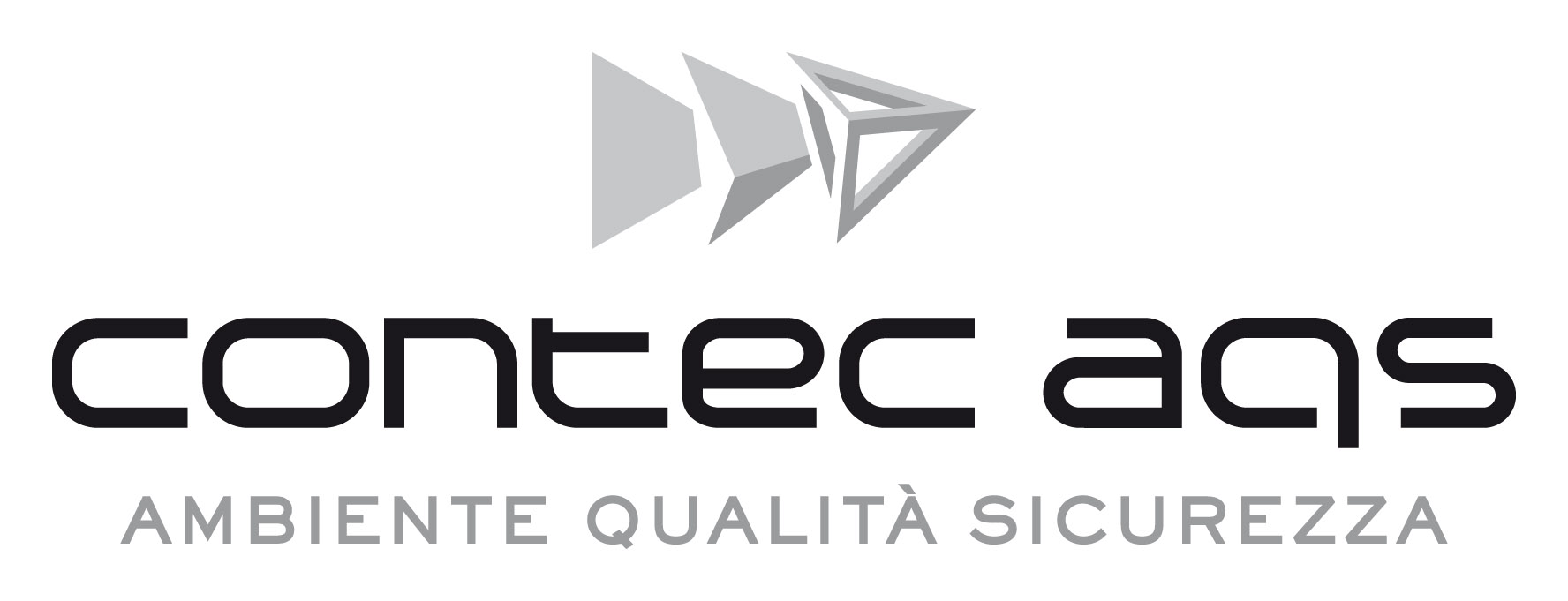
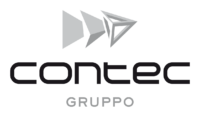