Fin dai primi dialoghi in materia e dalla prima comparsa a livello legislativo, il tema della ergonomia negli ambienti industriali è stato connotato da una forte interdisciplinarità: rappresenta infatti un ambito in cui si intersecano diverse discipline, ciascuna depositaria di un “tassello” necessario per raggiungere gli obiettivi dell’ergonomia, ossia le prestazioni del sistema analizzato e la soddisfazione dell’utente del sistema stesso.
Ergonomia negli ambienti industriali: una questione di sicurezza
In materia di salute e sicurezza sul lavoro, il rispetto dei principi ergonomici costituisce un preciso obbligo in capo al datore di lavoro: l’articolo 15 del D. Lgs. 81/2008, nel dettare le misure generali di tutela della salute e della sicurezza dei lavoratori, menziona il “rispetto dei principi ergonomici nell’organizzazione del lavoro, nella concezione dei posti di lavoro, nella scelta delle attrezzature e nella definizione dei metodi di lavoro e produzione, in particolare al fine di ridurre gli effetti sulla salute del lavoro monotono e di quello ripetitivo; […]”.
Naturalmente ogni luogo di lavoro rappresenta un unicum: se si pensa alle differenze che sussistono tra i luoghi in cui ciascun lavoratore esercita la propria attività lavorativa – non solo tra un’azienda e un’altra ma anche all’interno della stessa azienda – si intuisce subito la delicatezza della materia e la necessità di un processo articolato di valutazione dei rischi per rispettare a pieno il dettato normativo.
Le specificità degli ambienti industriali
L’ambiente industriale è solitamente caratterizzato dall’elevata presenza di macchinari e dalla conseguente commistione uomo-macchina nell’esercizio dell’attività lavorativa. Ciò comporta innanzitutto che l’obbligo della corretta ergonomia spesso si scontri con le operazioni di movimentazione manuale dei carichi (MMC). In tal caso, esistono idonee metodologie per affrontare il processo valutativo del rischio per il lavoratore.
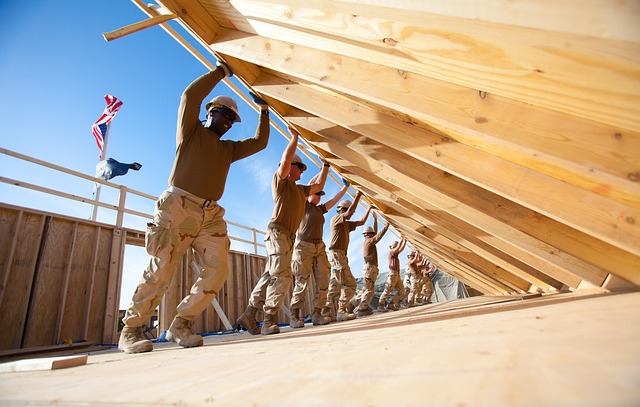
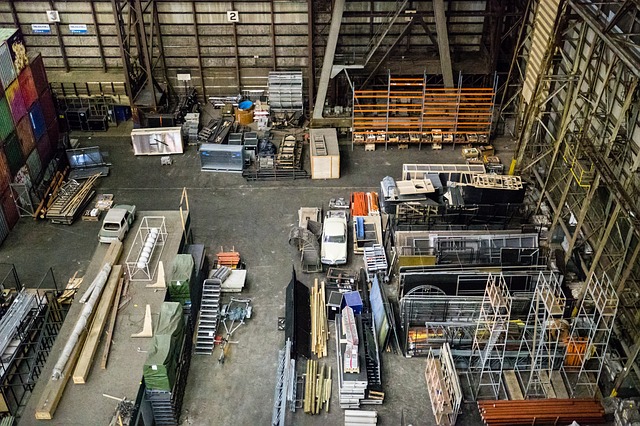
L’art. 168 del D.Lgs. 81/2008 rimanda all’allegato XXXIII, il quale a sua volta fa riferimento alla norma UNI ISO 11228, che determina gli elementi da considerare nella valutazione, i fattori di calcolo e i limiti massimali di carico per ciascuna condizione in analisi. In secondo luogo è necessario rispettare particolari accorgimenti anche nel dettare le regole di utilizzo delle macchine di lavoro, sulla base di quanto imposto dal D.Lgs. 17/2010, che recepisce in Italia la Direttiva Macchine 2006/42/CE.
L’Allegato I della Direttiva, “Requisiti essenziali di sicurezza e di tutela della salute relativi alla progettazione e alla costruzione delle macchine”, prevede il rispetto di diversi requisiti essenziali di sicurezza (RES). Il RES 1.1.16, dedicato all’ergonomia e applicabile a tutte le attrezzature di lavoro, macchine e impianti, afferma che nelle condizioni d’uso previste il disagio, la fatica e le tensioni psichiche e fisiche (stress) dell’operatore debbano essere ridotti al minimo possibile, tenendo conto di:
- dimensioni fisiche, della forza e della resistenza dell’operatore
- necessità di offrire lo spazio necessario per i movimenti delle parti del corpo dell’operatore
- necessità di evitare un controllo che richiede una concentrazione prolungata
- necessità di evitare un ritmo di lavoro condizionato dalla macchina
- necessità di adattare l’interfaccia uomo/macchina alle caratteristiche prevedibili dell’operatore
Ulteriori principi ergonomici vengono richiamati da altri requisiti essenziali di sicurezza e salute, ad esempio illuminazione (1.1.4), posti di lavoro (1.1.7, 1.1.8), dispositivi di comando (1.2.2), rischio di scivolamento, inciampo o caduta (1.5.15), accesso ai posti di lavoro (1.6.2).
Adattamento dell’area di lavoro
Il rispetto dei principi ergonomici, che come abbiamo visto sono richiamati da più di un testo legislativo, nonché l’obiettivo di una corretta movimentazione dei carichi, talvolta rendono necessaria una ridefinizione dell’area di lavoro. Le situazioni che si verificano in modo più ricorrente sono le seguenti:
Ridurre il rischio con la progettazione
Spesso il rischio ergonomico viene ridotto mediante l’inserimento nel parco macchine di un sistema di movimentazione dei carichi, che può favorire la velocità delle operazioni e vantaggi in termini di carico sollevabile e frequenza ammissibile, riducendo il carico che altrimenti grava sull’operatore. Tuttavia ogni stabilimento produttivo possiede proprie specifiche e particolarità.
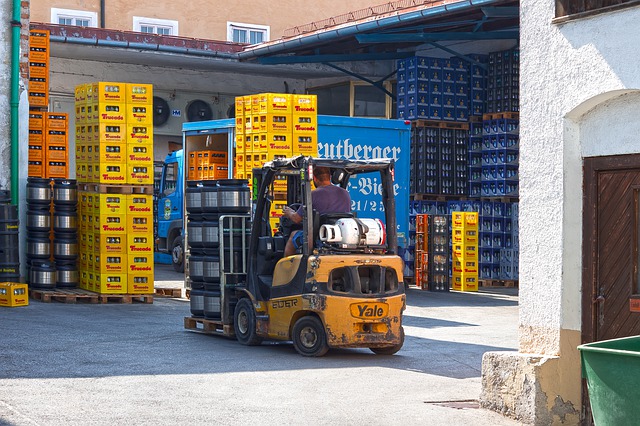
Le apparecchiature presenti sul mercato possono quindi risultare inadatte, comportando la necessità di avere attrezzature auto-costruite, progettate su misura. In tal caso l’imprenditore diventa costruttore a tutti gli effetti, soggetto agli obblighi e ai requisiti tecnici richiesti dalle normative, compreso l’obbligo di marcatura CE della macchina.
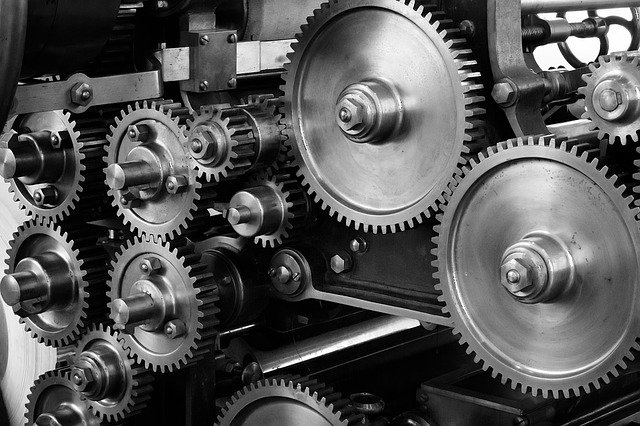
Per la maggior parte di queste attrezzature, inoltre, deve anche essere previsto un piano di verifiche, ispezioni, controlli periodici annuali e straordinari. Una soluzione mirata e personalizzata può rappresentare la modalità migliore per rispondere alle molteplici esigenze dimensionali e di portata, a garanzia della conformità agli standard richiesti dal sollevamento e della rispondenza ai requisiti di sicurezza.
Articolo dell’Ing. Luca Reppele, Direttore Tecnico di Contec Industry.
SERVIZI INGEGNERISTICI PER LE AZIENDE
Il Gruppo Contec aiuta le organizzazioni a realizzare progetti e gestire gli investimenti negli ambiti ingegneria e progettazione civile ed industriale. Fornisce soluzioni innovative e integrate per consentire ai propri partner di concentrarsi sul proprio business.